- Amanda
- June 12, 2017
6 ways to improve rail maintenance productivity
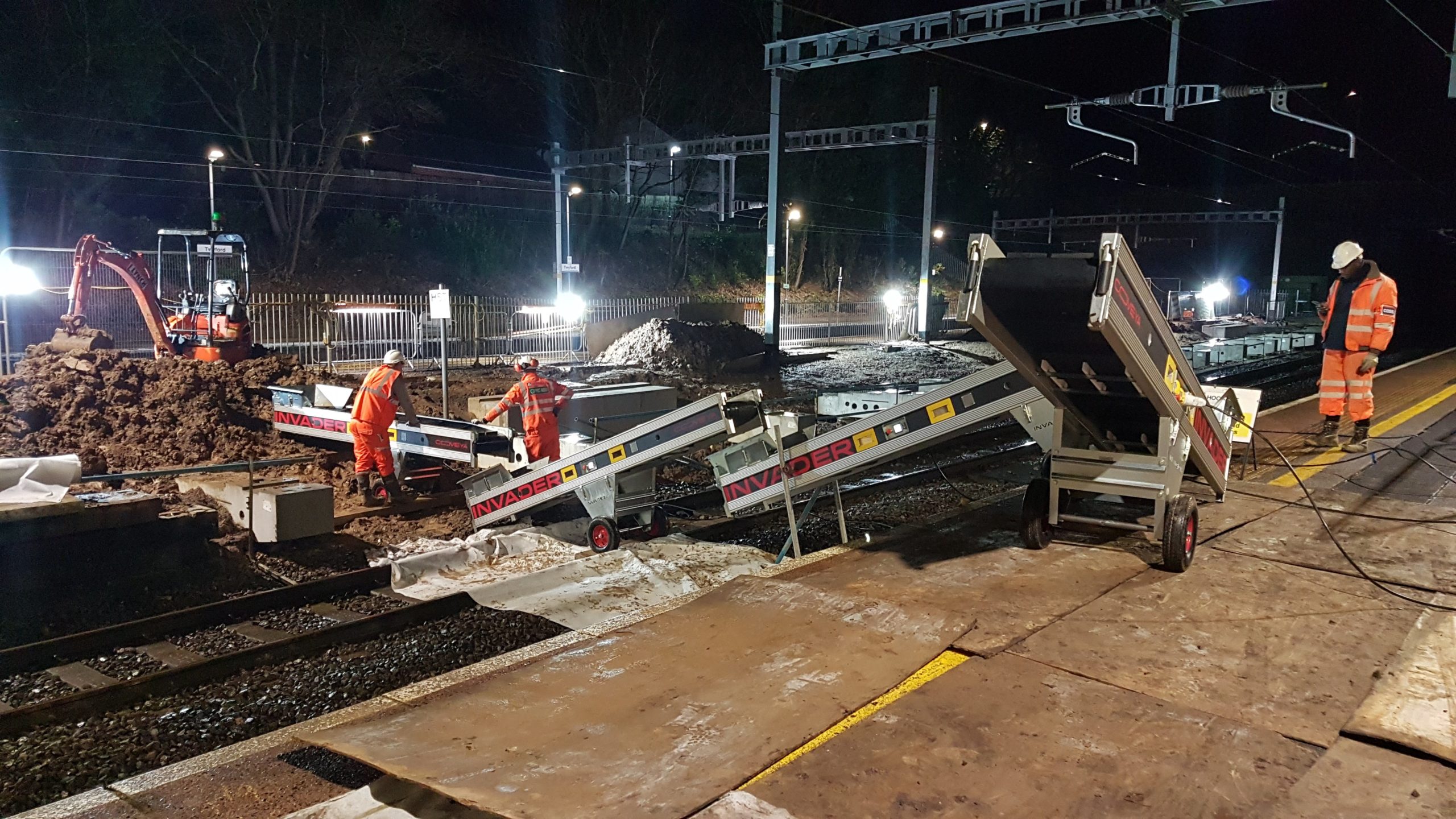
With extremely tight deadlines when it comes to managing rail maintenance and construction projects, saving time and increasing productivity is key. Yet with health and safety risks, overcrowded machinery, and disruptions to train services, it’s difficult to improve efficiency while maintaining a safe working environment.
Conveyor belts turn time-consuming manual and plant labour into an automated highly-efficient process, improving productivity and reducing time spent on track projects.
To help you make the best use of your conveyor belt, we have put together a guide on how they can assist you and help you to meet deadlines on your rail project.
1. Conveyors reduce health and safety risks
Our railways here in Britain are amongst the safest and most reliable in Europe, and our rail projects are required to meet stringent standards to keep them that way. Using conveyor belt systems reduce the health and safety risks associated with manual handling and unsociable working hours and make it easier to move equipment even in difficult environments.
For example, where improvements must be made to underground track lines and stations, restricted space and limited access sites can make heavy machinery unsuitable for materials movement. The solution lies with conveyor belts! By navigating stairways and other limited access obstructions, conveyors can make awkward work spaces work with ease.
A lightened, less labour-intensive workload means workers experience less mental and physical fatigue and benefit from increased concentration and better judgement. And with their work directly affecting onsite safety, it’s vital that workers maintain focus and stay alert at all times.
2. Conveyors save time
With ever-tightening deadlines on track possession, making the best use of this time is crucial. Conveyors optimise project time and improve onsite productivity by eliminating duplication of work and adding to a more reliable and efficient service.
Manual labour causes significantly lower productivity rates, and many rail companies are scrambling to save seconds by optimising one digger over another. This is where conveyor belts change the game, offering more flexibility and manoeuvrability for each project. Conveyors provide a continuous loop with a loading surface that is available 100% of the running time, transporting materials to and from the track quickly and efficiently.
3. Conveyors save money
Less time spent on a project usually results in lower costs, and reducing the number of personnel and large plant needed onsite makes for a more cost-effective operation. Fewer workers result in fewer wages to pay, with smaller conveyors out-working up to three labourers and moving significantly more than linked site dumpers. While the time and money spent is reduced, the quality of the work remains high; all the positives of increased productivity, without any of the drawbacks. In addition, a single digger operative can still be effective with a conveyor, even if the rest of the team may be at home, mysteriously ill after last night’s big champions league match.
4. Conveyors deliver a higher output
With a conveyor system in place, 400-600m of track renewals can be completed in as little as eight hours with 2km of track ballast being cleaned per hour, in some cases! That rate of output is a lot quicker than more conventional methods. Conveyors can easily transport ballast and other materials to and from the site, even in difficult environments or where the site is obstructed. This increases productivity and output by streamlining processes and making it easier to access the tracks.
5. Conveyors save space
Diggers and other large machinery, need a lot of space to operate. For most rail projects, diggers will form a ‘production line’ to complete the work and pass loads between one another, often taking up space across adjacent tracks. This, in turn, can cause disruption to other train lines, even if the work being done does not directly affect them. Conveyors require a lot less space, meaning adjacent lines can remain open, causing less disruption and fewer delays to passengers.
6. Conveyors are reliable and versatile
Highly versatile, conveyors are built for the job at hand and suited to harsh environments. They don’t take sick days, don’t stop for lunch and maintain a steady rate of productivity throughout the day. In addition, unlike any digger or dumper, conveyors move in one direction 100% of the time – no wasted time with your bucket moving back and forth.
Keep your conveyor belt well-maintained and it will prove to be a reliable and sturdy tool to help you meet your rail project deadlines.
For further best practice guidance on working with conveyors in the rail industry, visit the Coveya Knowledge Base, or browse our full range of conveyors for rail track, ballast and demolition here.
Get in touch
Coveya offers a wide range of conveyors for rail track, ballast and demolition projects. Why not let Coveya see how much time and money you could save?