- Amanda
- July 25, 2018
Conveyor Hire: 5 Questions To Ask Before You Hire a Conveyor
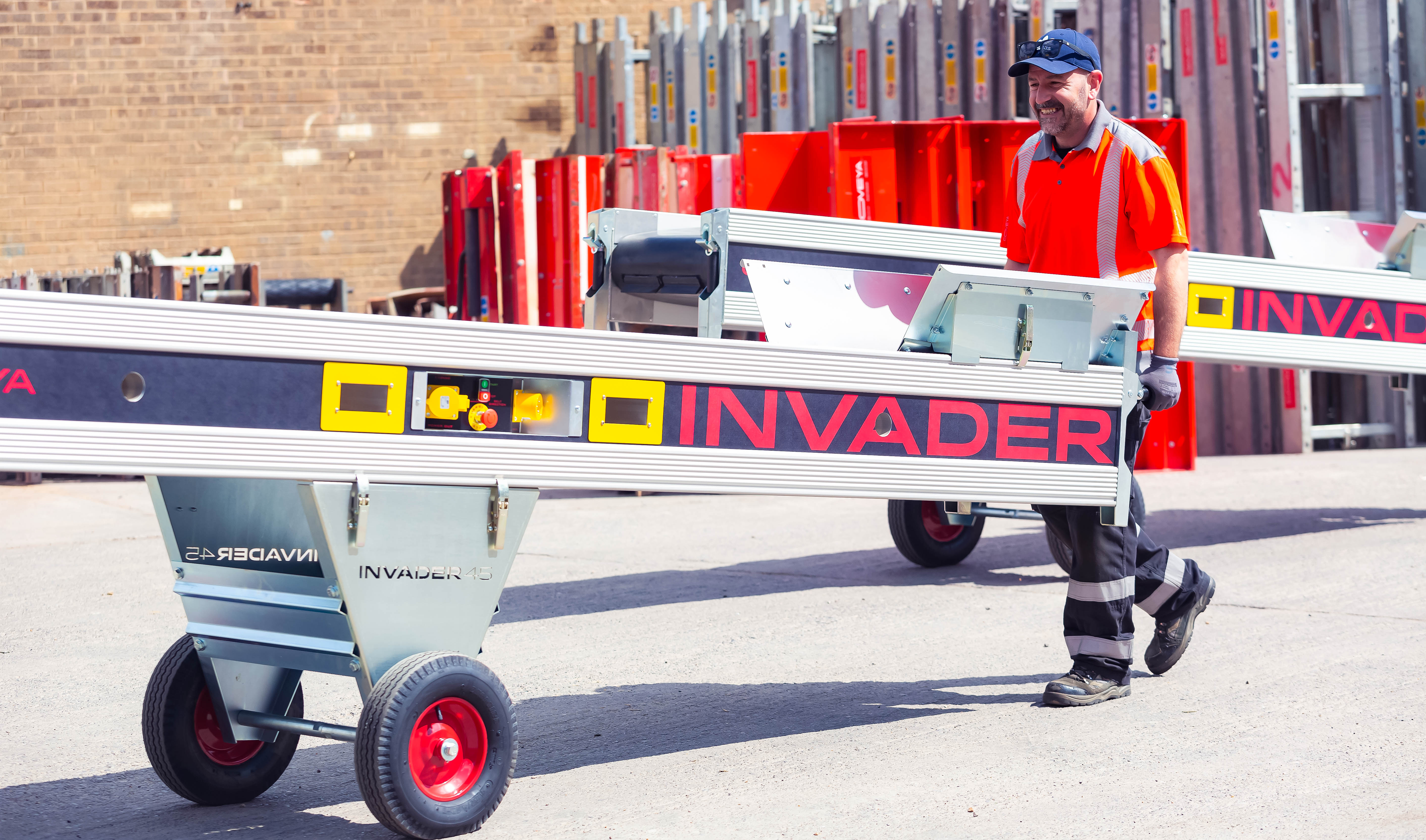
Conveyor belts can be used across such a huge range of applications that it’s essential to ask the right questions when looking for a reliable conveyor hire partner. From construction sites and recycling facilities to manufacturers and water treatment plants, getting the most efficient, most suitable and most cost-effective conveyor for the job is vital.
In this blog, the experts here at Coveya are going to discuss five of the most important questions to ask your conveyor belt hire company to help you get what you need, so you can make an informed decision before you hire. Let’s get started and help you find the conveyor system for your project.
1. What Type of Conveyors Do You Have?
Whether you know a little or a lot about conveyor belts, establish with your chosen conveyor hire supplier what type of belts they can supply. From a scan of their website to talking to one of their engineers, you should be confident that they know their trade and have the variety and range of conveyors to meet your needs. Modular conveyors like Easikit™ systems are ideal for many applications, but bespoke designs might better suit highly specialised industries.
Suppliers may sort their conveyors by industry to help you narrow down your choice, and some even provide a guide to choosing a conveyor to further help you decide.
2. What Conveyor Spec Do I Need?
If you’re a conveyor expert, you’ll probably be happy to spec’ your own equipment. If not, make sure your Specifying a conveyor system is a critical step in ensuring your conveyor hire delivers the results you need. What type of materials are you likely to be moving, and how much of it do you need to move in terms of weight and volume? How are you loading the materials? What conditions does the belt need to operate in? Does the job require specific features, such as chevron belts for inclines or wider belts for high-capacity loads?
Not sure? Not a problem, as any decent supplier will offer a robust specification process where a dedicated engineer will look at your project and find the perfect machine for the job. Knowledgeable suppliers will also consider factors like power supply availability and the method of loading, making your conveyor belt hire as easy as possible.
3. How Often Are the Conveyors Maintained and Serviced?
Put simply, well-maintained systems are more reliable, leading to smoother operation, improved productivity and most importantly eliminating downtime. A poorly maintained conveyor can lead to breakdowns, delays and increased costs. Reputable conveyor belt hire suppliers, like us here at Coveya, always have thorough maintenance procedures to keep equipment in top condition – hire a conveyor from us, for example, and we can perform on-site servicing every four weeks, carrying out any maintenance and replacing wear parts free of charge and as part of the hire agreement.
As long as your supplier carries out regular inspections and servicing, your conveyor hire should perform flawlessly and without unexpected issues suddenly cropping up and derailing your project. Choosing a supplier with a proactive approach to maintenance gives you peace of mind and ensures your project stays on track.
4. Do You Offer Training?
When hiring a conveyor, ensure the supplier offers training to ensure its safe and efficient use. Proper training equips your team to set up, operate and maintain the conveyor correctly, reducing downtime and errors. Coveya provides basic training alongside installation, alongside documentation, so operators understand how to maximise throughput, handle materials effectively and resolve any minor issues. On top of this, our knowledge base contains all the info you need to get the best from your conveyor hire, including how to use a conveyor safely.
Regular training also enhances safety and prolongs the equipment’s lifespan. With Coveya’s expert support, your team will gain the confidence to use the system efficiently from day one, ensuring your project stays on track with minimal disruptions.
5. What Will You Do if the Conveyor Breaks Down?
Breakdowns can be a major setback during a project, so it’s crucial to know how your supplier will respond if issues arise. A reliable conveyor hire provider should offer prompt support, including on-site service engineers and access to spare parts, to minimise downtime. Coveya have a team of engineers available throughout the whole of the UK that carry out proactive servicing aswell as responding to breakdowns at short notice.
Understanding how your supplier handles repairs is essential. Do they have a dedicated support team? Can they quickly provide parts or replacements? Coveya offers prompt on-site servicing and a range of maintenance resources, including videos, to help your team address minor issues and keep operations running smoothly. Choosing a conveyor belt hire supplier with proactive support ensures minimal downtime and keeps your project on track.
Find the Right Conveyor System for Your Project by Contacting Our Expert Team
Choosing the right conveyor system doesn’t have to be complicated – our expert team at Coveya is here to guide you every step of the way. When you need advice on your conveyor belt hire options, we’re ready to help you find the perfect solution for your project. We offer free site surveys, tailored recommendations and exceptional customer support to ensure you get the most out of your conveyor system.
Contact us today to discuss your needs or arrange a free site visit. Call 0808 501 5763, email support@coveya.co.uk or visit our contact us page to get started.